We could be months away from driverless semi trucks on Texas freeways
I visited two startups working to bring driverless technology to long-haul trucking.
I’m a journalist with a master’s degree in computer science. This week I’m publishing five in-depth articles that will provide a 360-degree understanding of the self-driving industry. I’m calling it Autonomy Week. Subscribe now to get future articles directly in your inbox.
On a sunny morning in December, an 18-wheeler will pull into a truck depot in Palmer, Texas, just south of Dallas. The driver will step out of the cab and help transfer his trailer to a second rig outfitted with powerful sensors.
This second truck will head south on Interstate 45 toward Houston. It will move cautiously, mostly cruising in the right lane at 65 mph despite the 75 mph speed limit.
After three and a half hours, the truck will exit the freeway in Greenpoint, a neighborhood in the north of Houston. It will proceed to a second truck depot, where the trailer will again be transferred to a new rig. A different driver will get in and haul the cargo to its final destination a few miles away.
Trucks travel the 200 miles between Dallas and Houston all the time. But there will be something special about the middle leg of this trip: There will be no one in the vehicle.
A startup called Aurora has spent seven years—and hundreds of millions of dollars—preparing for this driverless trip, which it hopes to complete before the end of the year. Last month, I met with Aurora co-founder Sterling Anderson at the company’s office in Mountain View, California.
The office has glass-walled conference rooms and row after row of workstations. But it also has some things you won’t find at a typical Silicon Valley startup.
Anderson showed me a lab with machines to measure how well Aurora’s hardware copes with the temperature swings and vibrations it will experience on the highway. One machine shakes so hard it needs a separate foundation to prevent it from damaging the building.
In another lab, engineers were using silicon photonics to reduce the size and cost—and increase the reliability—of Aurora’s proprietary lidar sensors.
There was a garage with several Aurora trucks. Anderson pointed out that each truck had not one but two computers tucked behind the driver’s seat. Each computer had its own power and network connections, so that if one computer failed, the other could take over automatically.
“In a self-driving truck you no longer have the backup of a human,” Anderson told me. “So you have to make changes to the actuation architecture: steering actuators, braking actuators, and power architecture. You have to introduce redundancies on a number of different channels.”
“You can't have a single point of failure,” he said. “The changes required to the base truck go very, very deep.”
The stakes are high. If Aurora’s first driverless trip down I-45 goes well, there will be dozens, then hundreds, and eventually thousands, of trips like it. With hundreds of thousands of long-haul truck drivers in the United States alone, this is a huge and potentially lucrative market.
Large trucks are involved in thousands of fatal crashes every year in the United States, and driverless technology has the potential to prevent many of these crashes. But there’s also a risk that an Aurora truck could crash. A fully loaded semi truck weighs up to 40 tons, so if Aurora’s hardware or software malfunctions, the results could be deadly.
I’m impressed by how hard Aurora has worked to prepare for fully driverless operation. But I won’t be fully convinced of Aurora’s approach until driverless trips become a daily occurrence.
After all, there used to be many more startups working on self-driving trucks, including Embark, Starsky, Ike, and TuSimple. Most of these companies ran out of money before they could demonstrate their commercial viability.
That’s not an immediate worry for Aurora, which just raised $483 million, extending its runway into 2026. And a few other driverless trucking startups are very much still in business:
Kodiak has signed contracts with industrial and military customers to help keep the lights on while it perfects its driverless technology for long-haul trucking.
Gatik is developing driverless box trucks to carry merchandise on shorter trips from distribution centers to retail locations for customers like Walmart and Kroger.
As we’ll see, both of these companies have already begun driverless testing in carefully limited circumstances. In the coming years, all three companies will need to scale up their driverless fleets and reach profitability—all without compromising on safety.
Roots at Carnegie Mellon, Google, and Uber
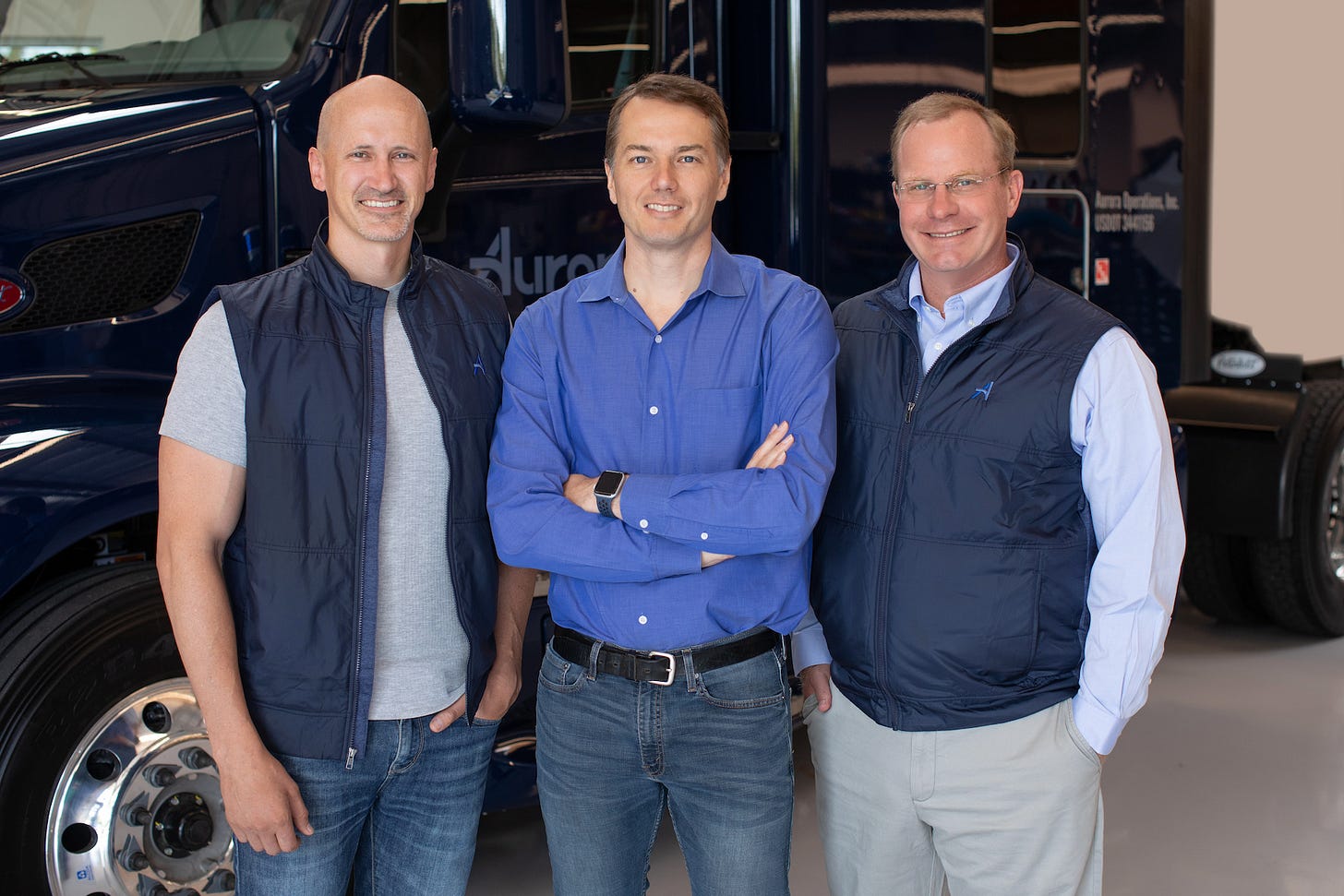
I visited Aurora and Kodiak on the same day. This was easy to do because they both have offices in Google’s hometown of Mountain View. That’s not a coincidence—both companies were founded by early veterans of Google’s self-driving car project.
Aurora CEO Chris Urmson was previously a professor at Carnegie Mellon, where he led the team that won DARPA’s 2007 Grand Challenge. He then joined Google’s self-driving car project in 2009 and became its leader in 2013. When Google rebranded the project as Waymo in 2016, it passed over Urmson and hired auto industry veteran John Krafcik to lead the new company. Urmson left Google in December 2016.
Kodiak CEO Don Burnette studied robotics at Carnegie Mellon before he joined Google’s self-driving car project in 2010. In 2016, he left with a fellow engineer, Anthony Levandowski, to start a self-driving truck startup called Otto. Six months later, Uber snapped the company up for a reported $680 million. Google sued, accusing Levandowski of taking Google’s trade secrets with him. Burnette quit Uber in 2018 to start Kodiak.
In 2017, Urmson co-founded Aurora with Sterling Anderson. Anderson previously led Tesla’s Autopilot program but clashed with Elon Musk over Musk’s unrealistic timeline for full self-driving technology. Aurora’s third co-founder was Drew Bagnell, a Carnegie Mellon professor who Uber hired to lead the perception team on its self-driving project.
In March 2018, an Uber self-driving vehicle struck and killed pedestrian Elaine Herzberg in Tempe, Arizona. Uber’s self-driving effort never really recovered from this setback. In 2020, Uber sold its self-driving project to Aurora in a stock swap that made Uber Aurora’s largest shareholder.
Kodiak: Aurora’s scrappier rival
The pedigree of Aurora’s founders enabled the company to raise $530 million in 2019. Uber injected another $400 million into Aurora as part of that 2020 deal, and the company has raised more than $1 billion since then.
Kodiak is a comparatively modest operation, having raised $40 million in 2018 and $125 million in 2021. This difference was obvious when I visited the two companies’ offices. Aurora’s office in Mountain View is about three times larger than Kodiak’s. And while Kodiak is based in Mountain View, Aurora has an even larger office—its headquarters—near Carnegie Mellon University in Pittsburgh.
In total, Kodiak has 210 employees, compared to 1,700 at Aurora.
The huge disparity in financial resources has driven the companies to adopt different business strategies.
For example, Aurora has acquired not just one but two startups to help it develop lidar-on-a-chip technology tuned for long-haul trucking. Lidar sensors create three-dimensional “point clouds” by bouncing lasers off nearby objects and measuring how long it takes for the light to return.
Typical lidar sensors have a range of around 200 meters. For a truck traveling 65 mph, Anderson told me, that was equivalent to driving through “a dense fog.” Aurora’s FirstLight lidar has a range of 500 meters. That gives Aurora’s self-driving trucks plenty of warning about upcoming hazards.
In contrast, Kodiak uses off-the-shelf lidar sensors developed by third parties.
“It’s very expensive to build your own lidar system,” Kodiak CEO Don Burnette said in a March interview. “And the probability is low that your lidar and the team that you’ve hired to build it is the best of the best.”
“We’ve worked with every manufacturer that you can probably name,” Burnette added. “If some new entrant comes along with a better sensor, we’re able to swap to that sensor.”
Aurora has spent years collaborating with PACCAR (which makes Kenworth and Peterbilt trucks) and Volvo to integrate Aurora’s technology directly into their vehicles.
In contrast, Kodiak has a more modular design that packs all of the sensors required for autonomy into a truck’s mirrors. These SensorPods make it easier for Kodiak to integrate its technology into a wide range of vehicles. The SensorPods also simplify the process of calibrating the sensors once they’re installed on a vehicle.
On the other hand, the lack of deep integration with any specific truck model may mean it will take longer for Kodiak to scale its technology to thousands of vehicles, since trucks won’t come off assembly lines with Kodiak technology built in.
Ample financial reserves have allowed Aurora’s engineers to keep their heads down for more than seven years preparing for a big commercial launch. Kodiak doesn’t have this luxury and has had to look for short-term revenue opportunities.
In 2022, Kodiak signed a $50 million contract to help the US military improve its own autonomous capabilities. During my visit to Mountain View, I saw Kodiak’s first military test vehicle, a Ford F-150 that had been equipped with Kodiak’s SensorPods. The long-term plan is for Kodiak to supply its sensors and software to another contractor who will incorporate them into vehicles designed for military use.
Recently, a fully driverless Kodiak truck began hauling sand in the Permian basin of West Texas. The customer is Atlas Energy Solutions, which supplies sand used for fracking in the region. Operating on private, leased roads at a maximum speed of 20 miles per hour gives Kodiak a chance to test its technology in an environment with relatively few pedestrians and other obstacles. It also gives Kodiak a chance to harden its sensors against dust storms and other harsh weather conditions.
“One of the big pushes recently from the investment community is to show that autonomous driving can be profitable,” Kodiak CTO Andreas Wendel told me. “That's how we got from pure over-the-road trucking into defense and industrial—because those are near term revenues.”
Those revenues will allow Kodiak to continue improving its technology and preparing to eventually put driverless trucks on public freeways.
Gatik’s short-haul strategy
Gatik made an early decision not to focus on long-haul trucking.
“It's a mass and velocity problem,” said Gatik CEO Gautam Narang in an interview last year. “You have this 80,000-pound truck driving down the highway at let's say 75 or 80 mph, you have to be damned sure that the system is perfect before you can pull the driver out. Companies have struggled with that.”
So Gatik decided to focus on a segment of the trucking industry that posed fewer technical challenges.
“Our trucks are smaller in size,” Narang said. “The routes are shorter. We have the flexibility and the luxury to choose the safest and the easiest possible routes.”
Gatik executive Philip Reinckens explained the company’s strategy to me in an August interview. Retailers hire Gatik to carry merchandise between distribution centers and retail stores. Gatik chooses routes that avoid trouble spots like schools and fire stations.
“Instead of doing an unprotected left turn, our truck may take three right turns,” Reinckens told me.
In 2019, a Gatik truck began driving a route near Walmart’s headquarters in Bentonville, Arkansas. Walmart stores need merchandise delivered every day, so Gatik got to drive the same route over and over again. After two years, Gatik felt confident enough to remove the safety driver from that particular route.
In 2021, Gatik published a press release about its first driverless route, which was “moving customer orders on a 7.1-mile journey between a dark store and a nearby Neighborhood Market in Bentonville.”
The most direct route between those two points on the map is only 1.8 miles. However, the Gatik truck doesn’t take a direct route. For example, it drives in a big rectangle around the campus of Northwest Medical Center, doubling the driving distance but avoiding a left turn.
So that 7.1-mile figure must be the round-trip distance once you factor in all those detours.
Gatik has taken a similar approach with more recent customers, using a safety driver at first and then removing the driver once it was confident its software could handle a route. Reinckens told me that Gatik is now able to remove the safety driver after driving a route for a year, half the time of that original Walmart route.
Gatik just raised $30 million, and the company says its customers have signed contracts worth $200 million “over the next couple of years.” So the company has big expansion plans.
My big worry about Gatik is whether its software is overly tuned to the specific routes where its trucks operate. Over the years, I’ve seen a number of startups train their software for a specific set of routes and then find it doesn’t generalize easily to other routes. The fact that Gatik spends a year training its trucks for each new route suggests that the company’s software might be brittle in this way. But it also might not be—we’ll just have to see how quickly the company grows in the next few years.
Dealing with worst-case scenarios
I’m generally impressed with the work these companies have done, but it’s still a pretty big leap to put a driverless truck onto public roads—especially at freeway speeds.
Waymo started out offering a driverless taxi service in the suburbs of Phoenix. Perfect weather, few pedestrians, and wide, well-marked streets made this a particularly easy environment for self-driving cars to navigate. Later Waymo expanded to residential San Francisco, then to downtown San Francisco, and then to the Phoenix airport.
It was only earlier this year—after years and tens of millions of miles of testing—that Waymo started putting its vehicles on freeways with no safety driver.
Evidently, Waymo considers freeways to be one of the most challenging environments for self-driving technology. And I think I know why.
When deploying a new self-driving vehicle, it makes sense for extreme caution to be the default. If a vehicle encounters a situation it doesn’t understand, it can come to a stop and request remote assistance. This can be annoying to other drivers—and indeed, many people got annoyed at Waymo and Cruise’s cautious driving last year—but it avoids crashes that could occur if a driverless vehicle proceeded into a situation it didn’t understand.
This cautious strategy is harder to implement in a freeway environment. As Gatik’s Gautam Narang put it, it’s a mass and velocity problem: It takes several seconds to come to a stop from 65 miles per hour, especially when you’re driving an 80,000-pound truck. And even if slamming on the brakes on a freeway doesn’t cause a pileup, it’s likely to cause a traffic jam.
So safely launching a driverless truck on the freeway is significantly harder than launching a driverless taxi on quiet residential streets. Aurora and Kodiak’s trucks can’t just slam on the brakes if they encounter a situation they don’t understand; they need the ability to reach a safe stopping place—like a wide shoulder or exit ramp—that might be a mile away.
Sterling Anderson told me that Aurora has taken several precautions to deal with a situation like this. As mentioned previously, Aurora’s trucks have redundancies in the steering and brake actuators, power systems, computer systems, cameras, and so forth. If one of these components fails, it should be able to gracefully pull over to the side of the road.
Even if both onboard computers fail, Anderson says, Aurora’s trucks have another failsafe.
“We've got a lower level system control interface that is caching a safe trajectory at any given point in time,” Anderson told me. “At the brainstem level, so to speak, this system is able to get the vehicle to a safe state.”
This was a good answer, and it may be the best any company can do. Still, there’s always a risk that a system this complicated will work in ways you don’t expect—especially the first few times it’s put to a real-world test without a human backup.
The key thing to remember, however, is that not deploying self-driving technology is also risky. Nearly 6,000 people were killed in crashes involving large trucks driven by humans in 2022. At scale, self-driving trucks should reduce this number significantly.
Aurora has conducted simulations of dozens of fatal crashes in California and Texas and concluded that the Aurora driver would have avoided all of the crashes where the truck was at fault.
Of course, we should only give so much weight to a theoretical exercise like this—especially one conducted by Aurora itself. But real-world data from Waymo paints a similar picture: Over Waymo’s first 22 million driverless miles, Waymo’s vehicles got into serious crashes three to six times less frequently than human drivers in the same areas.
If Aurora’s software performs this well, it could easily save thousands of lives over the course of the 2030s. And the only way to get there is to let Aurora take its first driverless trip.
My interview with Sterling Anderson
Below is a transcript of my August 12 conversation with Aurora co-founder Sterling Anderson, edited for length and clarity. It’s exclusively available for paid subscribers.
Keep reading with a 7-day free trial
Subscribe to Understanding AI to keep reading this post and get 7 days of free access to the full post archives.